e-Mobility Engineering Article Focuses on Modular Batteries
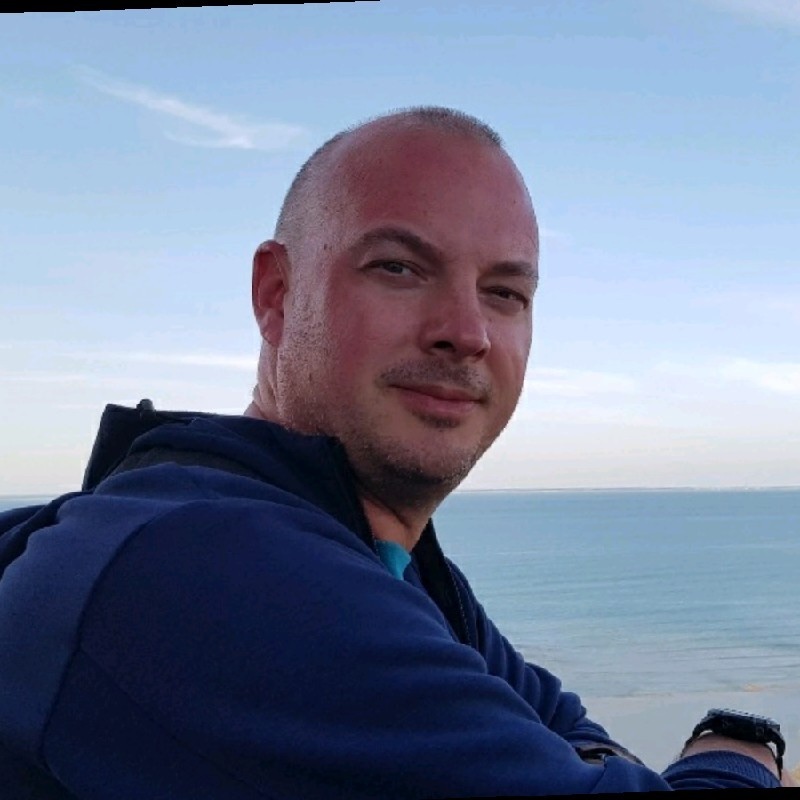
Contributor to e-Mobility Engineering Peter Donaldson’s recent article “Modular batteries” featured expert Seth Yates, head of product for Turntide, as a subject matter expert. According to the article, “Modular battery systems remain an essential component of e-mobility, offering unique advantages that complement recent advancements in cell-to-pack (C-t-P) technologies. While C-t-P designs optimize energy density by eliminating modules, modular batteries provide critical flexibility, scalability and serviceability. Engineers navigate complex trade-offs to integrate these features while addressing challenges in cost, weight, thermal management and recyclability.”
Seth Yates full commentary is detailed in the questions and answers below.
Much development has gone into eliminating the module from batteries to increase overall energy density; what advantages do module-based batteries retain over these technologies?
Modular batteries allow electric vehicle (EV) designers of lower volume applications to rapidly electrify their products using ready-certified designs. The plug-and-play solutions offered by modular battery technology allow for flexibility of application. While a modular design will not compete with a fully bespoke solution in terms of overall energy density, the advantage is seen in time to market and is often a lower cost solution for companies that do not have the budget or resources to design in-house bespoke solutions. They also allow easier distribution across an application, saving two to three custom systems to be designed.
How is the industry thinking about the role of modular batteries and the modules themselves in e-mobility applications evolving?
Modular batteries will play a vital role in the rapid transition to electrification for many smaller manufacturers that do not have the in-house resources or budget to develop a bespoke solution. They allow them to rapidly retrofit existing vehicles without the need for a new design for the electrified platform.
What are the most important engineering trade-offs that engineers face when developing battery modules?
Engineering trade-offs are reduced energy density and increased total system cost in modular designs.
Cell chemistry aside, how is the technology being packaged into battery modules for e-mobility applications changing?
Cell formats can be a significant factor when designing modular batteries. Cylindrical cells in larger formats are becoming standardized across the automotive energy sector and these can provide very cost-efficient solutions with high levels of safety. Pouch cells are often still preferred if battery weight is a driving factor.
In what ways does cell chemistry influence module design?
Lithium iron phosphate (LFP) cells are attractive for EV applications because of their lower costs and higher cycle life. The low operating voltage and low energy density of LFP chemistry means that more cells need to be fitted per module to achieve the same voltage and kilowatt-hour rating of the pack.
What degree of self-sufficiency is practical for modules, and what services, if any, will always have to be provided at pack level?
Basic voltage, current and temperature protections are available with modular batteries. However, for a system-cost perspective, it is better to provide the additional control features externally to the modular pack and only have one of these in the complete vehicle system. Otherwise, the customer is paying for this functionality for each battery module that is fitted to the vehicle.
How is the provision of safety mechanisms, such as thermal fuses, venting systems, cut-off mechanisms, at module level developing?
Managing thermal runaway and ensuring that battery packs meet the increasing demands from the safety standards are always challenging. Each design aims to improve on the performance of its predecessor, so a lot of rigor goes into designing and improving the safety systems used in the packs.
What are the options for incorporating thermal management into modules?
Where applications demand it, battery modules can have thermal management designed as part of the module. However, interconnection of the cooling system can be complex with multiple connections.
In modules designed to allow easy expansion or contraction of battery capacity, how does this affect energy density?
Overall energy density is compromised in a modular battery solution because of increased packaging/housing materials. This is countered by lower development costs, faster product development, and system flexibility.
What trade-offs have to be made in designing a module for integration into different vehicle architectures?
Other than overall energy density (volumetric and gravimetric) and selecting a specific shape format, no other trade-offs are required. Cell chemistry is critical when designing an optimized system, so engineering modules and packs that are cell agnostic is not likely to be practical.
In what ways are battery management systems evolving with advances in module technology?
There are two main architectures: A separate, master controller outside the modular packs or every modular pack having a master capability and configured for individual nodes. The first architecture offers greater flexibility and reduced system cost for applications with multiple modules.
What advanced concepts in modular battery technologies can we expect to reach the market in the near future?
We have lots of exciting innovative technology in development, but we cannot discuss this in any detail at this stage. However, the technologies revolve around safety and ease of system integration.