Equipment Manufacturers Should Be Fully Embracing Advanced Technology
In today’s fast-evolving landscape, embracing advanced technology is no longer optional—it’s essential. Across sectors like construction, agriculture, e-mobility, marine, and industrial machinery, original equipment manufacturers (OEMs) face challenges on multiple fronts:
- Environmental regulations
- Shifting customer expectations
- Labor shortages
- Increased competition from startups backed by venture capital
To be successful, manufacturers are not just dabbling in innovation—they’re building entire divisions around it.
A Decade of Change & What’s Coming Next
During the past decade, the mobility industry has experienced several waves of transformation. Initially, a shift from mechanical to electrohydraulic systems occurred. Then came the rise of the Industrial Internet of Things (IIoT), data connectivity, and electrification. While the technologies themselves have matured, adoption remains uneven. Too often, organizations adopt tech piecemeal—replacing parts of a system without reimagining the whole vehicle or piece of equipment. This tiptoe approach causes missed opportunities, poor return on investment (ROI), and systems that fail to live up to their potential.
The Drivers Behind Technology Adoption
Electrification and IIoT are not just about efficiency anymore—they are being driven by broader forces:
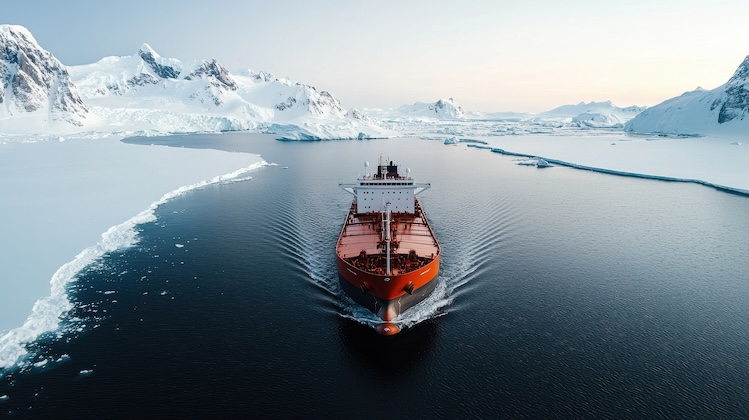
- Environmental regulations are tightening in many countries and several U.S. states. Whether it’s emission standards or noise restrictions in urban areas, OEMs are being forced to consider greener, quieter machines.
- Labor challenges are intensifying. An aging workforce and a lack of younger skilled workers entering the industry, make automation and digital tools more critical than ever.
- Safety and compliance demands are increasing. Connected systems allow for real-time monitoring and reporting, which supports safer work environments and faster incident response.
- Customer expectations are shifting. End-users—be it a city manager overseeing street sweepers or a turf maintenance crew working at 4 a.m.—increasingly expect quiet, efficient, tech-enabled equipment that minimizes disruption and improves operational insight.
- Investor interest is accelerating. Venture capital and private equity firms are actively targeting traditional off-highway and industrial sectors, viewing them as ripe for disruption. These new entrants move fast, often bringing innovative technologies to market without the constraints of legacy systems.
Why Partial Adoption Does Not Work
One of the biggest challenges that OEMs face is retrofitting existing platforms with new technologies. For example, in the electrification space, they often replace an internal combustion engine with a battery and electric motor but leave the rest of the system untouched. While this may work as a proof of concept or marketing exercise, it rarely delivers the full value of electrification.
In many cases, the best ROI from electrification or IIoT is only realized when the system is designed from the ground up. This includes rethinking how power is delivered and how data is collected, how the operator interacts with the machine, and how the machine is serviced.
For IIoT applications, the same principle applies. Without a clear business case—whether reducing downtime, improving service, or enabling predictive maintenance—connected technology becomes a cost center rather than a strategic advantage.
From Machine Connectivity to Business Transformation
Modern IIoT platforms do more than stream data from machines. They connect entire organizations. A structured, phased approach often yields the best results:
- Connect the machine – Capture meaningful, accurate data from the equipment in the field.
- Connect the business – Integrate the captured data with internal systems like an enterprise resource planning system, service platforms, and supply chain tools.
- Connect the ecosystem – Empower dealers, service centers, and end users with insights and tools that create value.
When done right, this transforms OEMs from product companies into technology-driven service providers. In fact, one example customer plans to grow its aftermarket parts and service business from 10% to more than 25% of total revenue by 2030—fueled entirely by connected systems, smarter design, and strategic use of data.
Electrification: A Catalyst for Smarter Machines
Electrification doesn’t just change how machines are powered—it changes how they are built, serviced, and upgraded. Electric machines support more advanced control systems, software-driven updates, and remote diagnostics. This makes them ideal platforms for delivering new business models like remote maintenance, software-as-a-service, and fleet optimization.
Even more compelling, connected electric machines allows for continuous improvement. Just like many passenger vehicles receive over-the-air updates, industrial machines can do the same—enhancing safety, efficiency, and operator experience without a hardware refresh.
The Power of Collaboration
One important takeaway regarding technology in anything that moves is the growing importance of collaboration and partnerships. No single company—no matter how large—has every component, technology, and insight needed to build the next generation of vehicles and equipment.
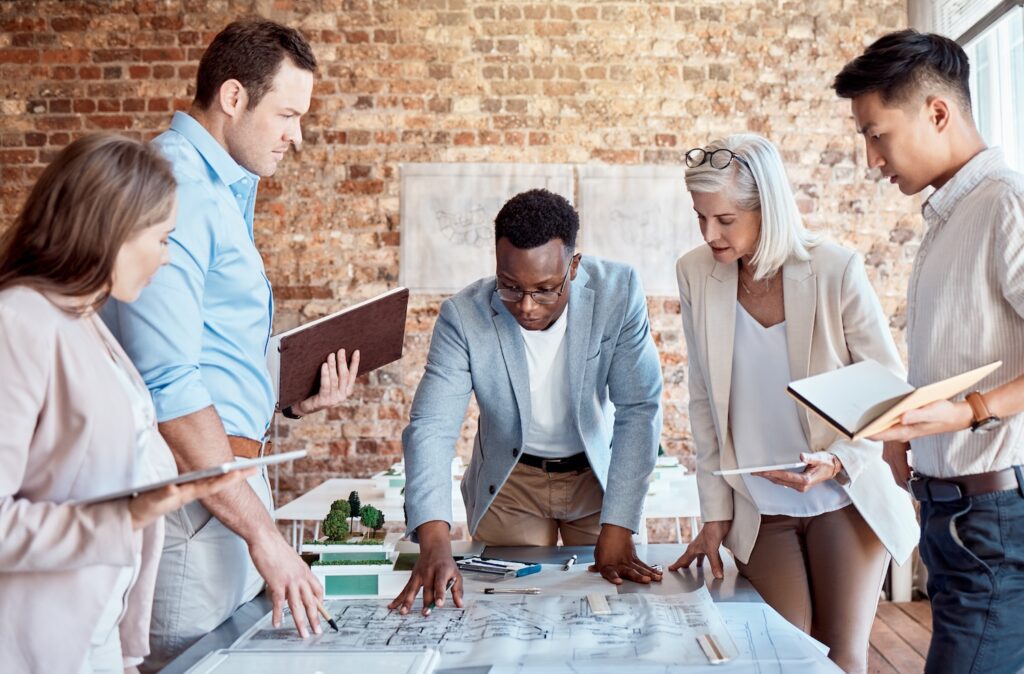
Instead, leading OEMs are building ecosystems that include:
- Component manufacturers that collaborate on interoperable systems
- System integrators and distributors who bring cross-industry expertise
- Technology vendors that provide platforms for connectivity, analytics, and control
- Service and dealer networks that ensure field performance and customer satisfaction
This collaborative model is essential for integration and scalability. When OEMs partner with technology providers who have already solved complex integration challenges, they reduce risk, speed up time-to-market, and improve reliability.
Building a Long-Term Innovation Strategy
Many of the most successful OEMs are taking a deliberate, long-term approach to innovation. They’re building dedicated teams and divisions focused on electrification, digital transformation, and product strategy. These teams are not side projects—they’re core to the organization’s growth.
One key differentiator: these companies collect real-world data first, then use that data to inform product design. By deploying IIoT systems on traditional machines in the field, they learn how those machines are used—then apply those insights to the design of the next generation.
This leads to more efficient, purpose-built electrified machines that are easier to operate, easier to service, and more profitable over time.
What’s Next? A Smarter, Cleaner, More Connected Industry
The next few years will be transformative for construction, agriculture, industrial, and e-mobility markets. Electrification, autonomy, connectivity, and data science are converging—reshaping not just machines, but business models, customer expectations, and value.
The good news? OEMs don’t have to do this alone. With the right partners, a clear strategy, and a willingness to rethink traditional approaches, they can accelerate their journey toward a smarter, cleaner, and more connected future.
Act: Start with a Roadmap
For OEMs who want to start or scale their technology adoption, the most important step is to create a roadmap. This includes:
- Defining the business case – What will the technology enable or improve?
- Assembling the right team – Who owns the initiative internally and who needs to be part of the team?
- Selecting strategic partners – Who can bring the expertise, tools, and support to ensure a strong, reliable end product?
- Designing from the ground up – How will the entire system be optimized?
- Planning for evolution – How will the machine and business model improve over time?
Conclusion
Innovation isn’t about bolting new tech onto old machines. It’s about reimagining what’s possible—from the factory floor to the job site, from the cloud to the customer. For manufacturers ready to lead, the opportunities are vast. However, the time to act is now. Companies that embrace this transformation today will define the industry tomorrow.
Learn more by watching this on-demand webinar, “Technology Readies the Mobility Industry for Changes,” presented by Joshua Felt and Adam Livesay.