Hitachi Rail Delivers a Hybrid Solution to Decrease the Emissions of Passenger Trains
As the U.K. moves closer to its 2050 net zero target, the need to decarbonize the country’s transport network is more pressing. Reducing rail emissions and supporting net zero has long been a priority for Hitachi Rail. Cutting-edge battery technology represents one way that Hitachi Rail can meet its sustainability goals. To make battery technology for the U.K. railways a reality, Hitachi Rail partnered with an experienced battery manufacturer.
The Challenge: A Retrofit Hybrid Solution to Decrease the Emissions of Passenger Trains
Hitachi Rail, a fully integrated, global provider of rail solutions wanted to lead the rail decarbonization movement by bringing a more sustainable electric rail system to market. By providing a hybrid solution to decrease passenger train emissions that could be retrofitted to existing trains, the team hoped to dramatically reduce carbon emissions without requiring a complete redesign of the trains.
Hitachi was looking for an innovative electrification partner who could work with them throughout the research and development process to produce integrated battery technology capable of delivering the energy needed without compromising performance, range, or carrying capacity. Hitachi Rail needed an experienced electrification supplier that understood cell chemistry and how to integrate battery technology into vehicle systems.
Finding the Right Electrification Partner
To reach the goal of decreasing the emissions of passenger trains, the Hitachi Rail team needed a partner with the right energy storage provider. The manufacturer needed an in-depth understanding of battery chemistries, knowledge of stringent rail standards, and experience creating large- scale battery systems. One team’s decades of experience with battery cell technology made them an ideal choice for the project.
This battery engineering team worked closely with Hitachi to understand the vehicle specifications; the train’s drive and duty cycles; regulatory specifications and safety concerns; and other project requirements, such as cooling and thermal management.
Battery Design & Electrification Expertise
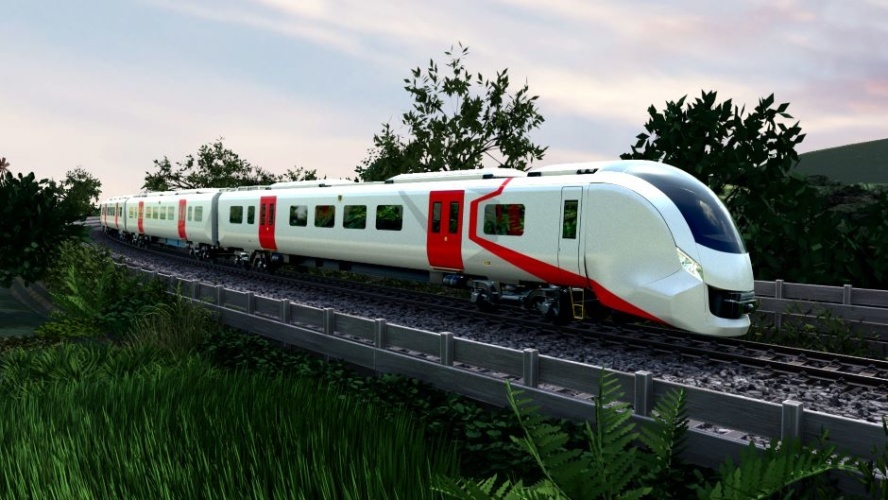
The partner needed to work with them through the research and development process to produce
integrated battery technology to deliver the energy needed without compromising performance.
Working with a team that designs, engineers, and rapidly manufactures innovative electrification solutions is important. Engineers have decades of experience, and use cutting edge tools and techniques to develop the electrification solutions of the future that accelerate manufacturers’ journey to electrification.
Battery Chemistry & Cell Module Selection
The battery manufacturer was able to help Hitachi Rail navigate the complex process of battery system design, evaluating cell chemistry options based on factors such as:
- Energy and power specifications
- Lifespan
- Safety
- Cost
- Fast charging capabilities
The system allowed the team to decrease the emissions of passenger trains, existing and new.
Industry Regulation & Safety Standards
Rail standards are some of the most stringent in the world. Because of this, adherence to industry regulations such as BSEN and IEC standards was another critical part of the battery project. The battery solution was designed to meet the following standards for rolling stock and railway applications:
- BSEN-62928
- BSEN- 62619
- BSEN-50155
- IEC-61508
The Hybrid Solution: A High-Performance Train Battery Pack with an Intelligent Built-in Battery Management System
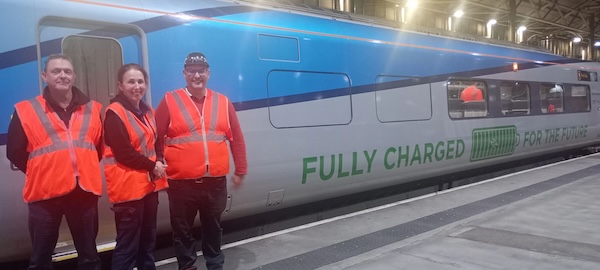
Delivering sustainable mobility solutions means having high energy density. The solution should also be a flexible and scalable modular design for rapid deployment. The Series system voltage is a 48-volt (V) to 630-V capacity and more than 750 kilowatts.
The partnership produced a high-performance rail application battery pack of 16 batteries with a nominal system voltage of more than 2,500 V, designed to last four years on arduous routes or up to 15 years on lighter routes. This modular solution is ideal for retrofitting existing trains and avoiding extensive reengineering or rebuilding of the entire train.