Advanced Inverter Technology Powers Last-Mile EV Delivery & Three-Wheel Vehicles in the APAC Region
Advanced inverter technology is improving efficiency and operation. Use of electric vehicles is growing in India and the Asia-Pacific (APAC) region. Like adoption in other areas, the first wave of electrification growth strong in light mobility, such as two-wheel; three-wheel; and light, four-wheel commercial vehicles.
Light mobility platforms focus on two key voltage architectures: 48 V and 96 V. Key demands for light-mobility, electric platforms in India include a high range achieved through high efficiency and optimum performance in harsh conditions in terms of thermal and ingress protection performance.
These smaller vehicles do not have a separate motor controller and dedicated vehicle control unit. They have one inverter or controller that manages the motor and vehicle controls like the lights and HVAC system.
This pivot toward sustainable electric solutions presents unique engineering challenges, particularly for vehicles operating in diverse environments with space constraints. Two prominent Indian manufacturers recently embarked on electrification journeys, each requiring specialized power control systems with minimal footprint and optimal performance for Indian road conditions.
Both manufacturers required inverters with exceptional characteristics: compact dimensions, low-voltage capabilities, and high power density. The systems needed to excel in applications operating in low-voltage architectures, a critical specification for their intended use cases. Through collaboration with the component manufacturer’s expert engineering teams, these manufacturers successfully implemented solutions that addressed their requirements.
The following case study examines how innovative power control technology helped transform a popular, last-mile delivery vehicle, highlighting the engineering challenges, implemented solutions, and resulting performance improvements.
Advanced Inverter Technology Improves Last-Mile Delivery
A leading commercial vehicle manufacturer in India sought to electrify its bestselling light commercial vehicle—a model with significant market share across the subcontinent. This electrification initiative represented the company’s first venture into the electric vehicle market, making the project both strategically important and technically challenging. The initiative required best-in-class performance on efficiency and range alongside additional provision of inputs and outputs to carry out bespoke vehicle control functions that manage the motor and specific aspects of a vehicle’s performance, handling, safety, or user experience.
The engineering team of the electric components manufacturer faced several constraints:
- The power control system needed to operate efficiently at 48 V or 96 V.
- Performance characteristics had to match or exceed those of conventional vehicles.
- The system required customizable software architecture to control the motor and bespoke vehicle functions.
- The solution needed to withstand diverse environmental conditions across India’s varied climate zones and landscapes.
The Solution
After evaluating multiple options, the manufacturer implemented an advanced inverter system that precisely addressed the requirements. It showed traceability between end-user and original equipment manufacturer (OEM) benefits and the controller’s features. The inverter had:
- Industry-leading power density
- Intelligent motor control algorithms that allow accurate control and high-efficiency operation
- User code features that empower and enable OEMs to develop and implement custom control features
These features allowed the customer to successfully integrate the motor controller, deliver best in class range performance though high efficiency performance of the motor controller, and implement all vehicle control and interfacing functions through the customizable user code feature
The Results
The implementation of this specialized inverter technology yielded substantial benefits:
- Successfully electrified the manufacturer’s bestselling commercial vehicle while maintaining its familiar form factor and utility
- Achieved power density metrics that outperformed competing solutions
- Enhanced operational reliability compared to alternative inverter technologies
- Maintained performance characteristics that matched or exceeded the conventional vehicle
- Simplified maintenance requirements, reducing total cost of ownership
The success of this project demonstrates how a manufacturer who configures their designs to the OEM’s specifications can deliver much more relevant engineering solutions than those offering off-the-shelf products. These principles ensured that the final implementation not only met but exceeded the manufacturer’s requirements, establishing a blueprint for future electrification projects across their vehicle lineup.
Commercial operators using these vehicles benefit from reduced operational costs, enhanced performance characteristics, and improved reliability—all while contributing to India’s sustainability objectives through reduced emissions.
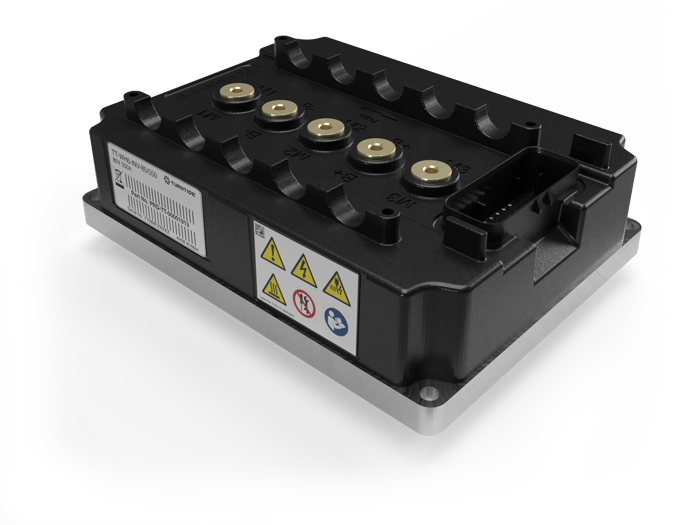
Three-Wheel Vehicles
Three-wheel vehicles in India that are used for passengers and cargo are moving to electric power. Three-wheel electric vehicles (EVs) can improve health because of lower noise, vibration, and harshness. Every 100,000 EVs can avoid about 32 tons of fine particulate matter across the vehicle’s lifetime.
The Problem
Three-wheel EV manufacturers needed to find a 48-V motor controller to improve the efficiency and operation of its vehicles. They required that the controllers be efficient and have scalable power levels to satisfy the many on- and off-highway applications that the vehicles are used in. In addition, the government mandate in India is to use equipment that is made in India.
The Solution
The manufacturer decided to use a motor controller that had been proven in field use for more than a decade. It incorporates in-demand features including multiple drivability modes such as a hill hold function, traction control, and throttle response.
Its optimized design delivers reliability in demanding applications.
The Results
Because of the motor controller’s scalability, the manufacturer achieved a range of improvements through rigorous testing and fine tuning of motor control algorithms and limits. In addition, the provider of the controller/inverter manufactures the components in India, which was important for many reasons.