Inverter Implementation Guide
Inverter integration is critical to ensure the efficient operation of electric and hybrid systems. After selecting a motor for an application, inverter selection can start. You then need to go through requirements gathering and assessment, pairing, inverter configuration (and customization), inverter integration, commissioning, and application sign-off before the inverter is in successful use.
When working with an inverter manufacturer, certain parameters are critical for inverter selection and implementation. Gathering this information should start early in the design process—ideally when building the application architecture concept. Aspects defined at this stage will narrow the list of appropriate inverters. Aspects include system direct-current (DC) voltage and motor type. For example, DC motors will not need an inverter.

The control algorithm required differs with the nature of the motor, such as interior permanent magnet motors or induction motors. Inverters may support only specific types of position sensor. Also important is the nature of the application; for example, does the inverter need to provide vehicle control functionality?
An inverter partner should be brought on at this early stage to:
- Help focus the requirements
- Hone the list of solutions
- Ensure that the correct details are captured
- Better understand how and why the inverter provides the right solution
Major Parameters for Inverter Implementation
Important parameters to consider before inverter implementation dictate its nature and major physical aspects as well as the larger portion of its capability. The first parameters used to help make an inverter choice include the motor’s number of phases, DC system voltage, and motor phase currents required to produce the desired torques.
The number of phases dictates overall inverter design. If wrong, the inverter will not be able to correctly operate the motor. Alternating-current motors for modern mobility applications are generally 3-phase.
Inverters are designed with certain components to cope with specific voltages. Higher voltages mean more expensive components. This design limits the voltage range over which the inverter can work. If the application voltage range is outside that of the inverter, system performance will be limited, component damage may occur, or the system may not function at all.
Higher phase currents require larger components, such as IGBTs, and more components, such as capacitors, to handle the increased electrical and thermal load. These may increase the cost of the inverter. To mitigate this, inverters are designed with specific current capabilities. If the current required to produce the desired torque exceeds the inverter’s capability, the system’s performance will be limited. This parameter is generally used up-front to select the manufacturer and model range.
Operating Currents
To select a model based on operating currents, consider how much phase current is required continuously (for 60 minutes or more—the equivalent of S1 when describing electric motors). S1, defined by BS EN 60034:2010 is operation at a constant load maintained for sufficient time to allow the machine to reach thermal equilibrium. Then consider how much peak phase current is required for short durations such as 2 minutes (the equivalent of S2 when describing electric motors).
S2 is operation at a constant load for a given time, less than that required to reach thermal equilibrium, followed by a time de-energized and at rest of sufficient duration to re-establish machine temperatures within 2K of the coolant temperature. The S2 duty cycle effectively measures the load capability for a short duration. Boost current is a term sometimes used to describe the absolute maximum phase current that an inverter can supply instantaneously.
Those who under-specify an inverter for the currents will limit system performance and may damage the inverter and the surrounding system. Over-specifying means significantly less chance for damage, but it could be a factor in increased manufacture and assembly costs and impact other aspects such as packaging.
Further Critical Requirements for Inverter Integration
Other critical requirements are:
- Ingress protection rating
- Temperature capabilities
- Cooling type
- Control functionality such as vehicle controller and functionality and simple CAN control
- Motor type
- Motor sensors
- Motor operating range
- Standard or regulatory adherence
These parameters ensure that the inverter selected is appropriate for the application, can perform correctly, and will fulfill the end user’s major requirements. Motor and motor control requirements include the motor type: Is it a permanent magnet or an induction motor? Is it surface permanent magnet or interior permanent magnet? Is it axial or radial flux?
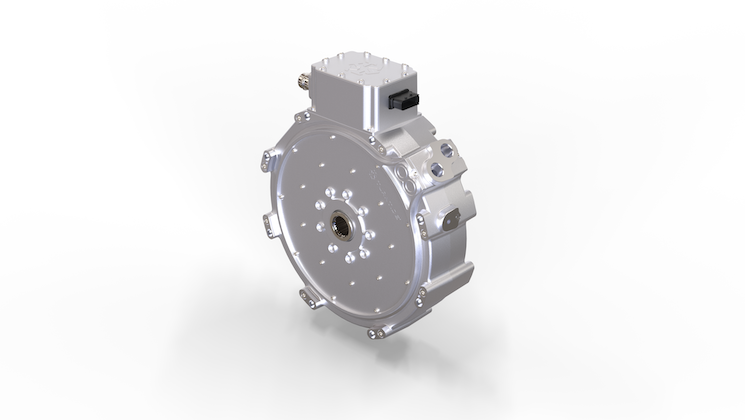
What speed and torque range will the motor need to output? How many pole pairs does the motor have? What type of position sensor does the motor have? Other considerations include the temperature sensor numbers and types.
Consider motor performance characteristics or tuning parameters such as back-EMF constant, torque constant, phase resistances, phase inductances, and short-circuit current.
Additionally, OEMs should understand their control requirements:
- Is vehicle control functionality such as throttle and brake inputs or forward/reverse switches required?
- Alternatively, will the unit be under simple CAN control?
- What is the communications protocol?
- Does the motor need to be under speed or torque control?
- Are any special functions required, such as hill hold or traction control?
Environmental Capabilities
Environmental considerations include what cooling system will the inverter have, air or liquid? What ambient air temperatures, coolant temperatures, flow rates, and shock and vibration will the inverter experience? Does the inverter require an ingress protection rating? Does the inverter need to meet any specific industry standards, regulations, or legislation?
In addition, altitude, air density, and temperature can affect the inverter’s overvoltage capability and safety.
Additional Information Needed for Inverter Integration
OEMs must also consider the type of inverter-motor pairing that is required. Will a simple and quick inverter-motor pairing—such as a geometric algorithm, which may get 80% to 90% of the full system capability—suffice? Or is the expectation for 100% system capability? Therefore, the requirement would be a fully defined characterization pairing.
What is the expected exact motor output profile in terms of power or torque against speed? Exact operating voltages—nominal and minimum/maximum—are important to be correct as they will impact system performance.
For any application, the inverter must work together with the motor to ensure that current and voltage limits are in place, and the system stays within the batteries’ charge and discharge current limits and over/undervoltage limits.
Customer Inquiry Form
A complete and accurate record of all requirements provides a common place where these details can be reviewed and agreed upon by both parties. This establishes a formal agreement for performance and functionality. It details a record of the capability versus the requirements and can identify gaps for which actions can be agreed to by the supplier and customer. Many inverter suppliers specify this information in a customer inquiry form.
This customer inquiry form is then used to help select a product that is appropriate, to perform configuration or required customization, and to detail the nature of the product compared to what is needed. Incomplete or inaccurate forms may mean an OEM does not get a product that fulfills all the requirements or performs as intended.
It also could mean that the inverter may receive damage or fail immediately or early because information was missing, and the correct solution wasn’t identified or selected. This could then mean the manufacturer’s application is unsafe, cannot be homologated, operates illegally, or is unreliable.
Therefore, not having all the required information could result in harm to humans or the environment; fines or other actions for breaching legislation; major revenue loss and negative public perception for the manufacturer. Lack of or incorrect information could also lead to wasted development time and costs, damaged supplier-manufacturer or manufacturer-end-user relationships, iterative and costly design processes, and limited system performance.