Why Voltage Matters
Inverters are critical components in nearly every modern power conversion system — from renewable energy installations to electric vehicles (EVs) and industrial automation. At their core, inverters convert direct-current (DC) voltage into alternating-current (AC) voltage and back again, enabling the use of stored or generated energy in a wide range of applications. They are responsible for the translation of power from the grid to a variable speed motor and back again. While much attention is paid to current, frequency, efficiency, and torque, one parameter is especially critical: voltage.
Fixed DC voltage not only dictates the power delivery capability of an inverter system but also has a profound impact on efficiency, thermal management, system size, and overall reliability. In this article, we’ll explore the pivotal role voltage plays in inverter design, why high-voltage systems are gaining momentum, and what that means for the future of electrification.
Understanding Voltage in Inverters
Why voltage matters, fundamentally, is because voltage is the electrical potential that drives current through a circuit. The DC voltage supply available in an inverter can be considered fixed, and within the inverter this voltage is switched in such a way that it becomes a polyphase (for example, three-phase) AC voltage of arbitrary magnitude and frequency at its output. The AC output is controlled by the inverter to suit the speed and torque requirements of the attached motor doing the demanded work. However the maximum output voltage that can be applied to the motor is generally limited by the DC supply voltage. Therein the DC system voltage choice cascades choices throughout the rest of the system.
The basic relationship between voltage (V), current (I), and power (P) is shown in this equation:
P = V x I
This equation underpins the engineering trade-offs between voltage and current, explaining another reason why voltage matters. Increasing voltage allows for a proportional reduction in current for the same power output—a concept that carries substantial implications.
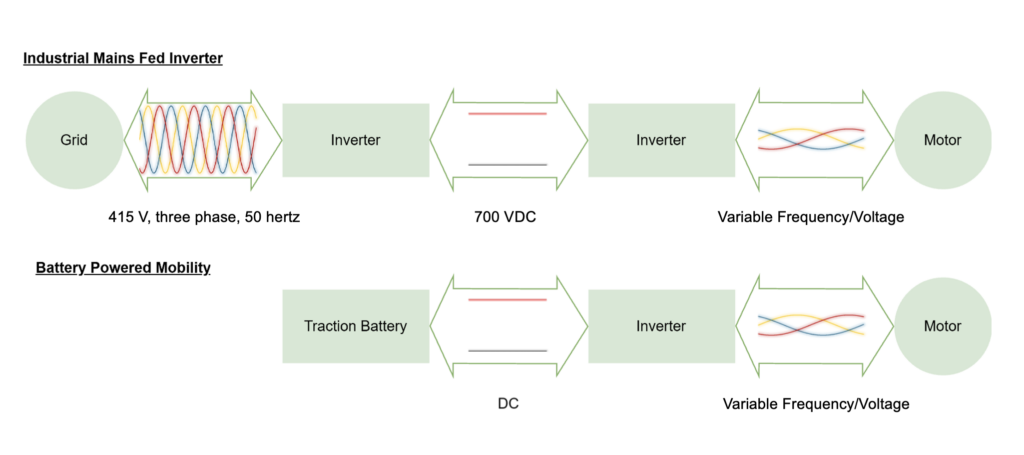
Reduced Current Requirements at Higher Voltage
Because raising the voltage reduces the current needed to deliver a given amount of power, the resultant lower current reduces I²R (a formula for electrical efficiency) losses, which are the resistive heating in cables and electronic components. This means that:
- Smaller power conductors can be used, reducing weight, space and cost.
- System efficiencies are improved, which directly translates to extended range.
- Components are subjected to less thermal stress.
- System designers gain flexibility in layout and packaging.
- Designers can capitalize on breakthrough technologies, such as wide bandgap power electronics, which can result in improved losses and higher switching frequencies.
Benefits of Lower Heat Losses & Improved Efficiency
Since current decreases at higher voltage for the same power, heat losses drop dramatically. This translates to:
- Improved inverter efficiency
- Lower cooling requirements
- Enhanced long-term reliability
Total Cost of Ownership
The comparison of lifetime EVs’ cost compared with their combustion power alternatives is the primary metric affecting the shift toward electrification. Typically, this doesn’t include subsidies for the reduction of carbon dioxide emission rates, or if it does, it can artificially skew the total cost of ownership (TCO). The choice of voltage has a big impact on TCO and is, in any commercial mobility electrification project, the primary measure of success. Some measures include:
- Improved system efficiency increases range and runtime for a given capacity, enhancing the return on investment.
- Reduced battery capacity (affecting cost) for a given range helps offset some overall costs for the same specification at lower voltage.
- Reduced charging times increases equipment availability.
Therefore, when OEM engineers and designers select the voltage, they must consider many unintended consequences of this design choice to achieve the most beneficial outcomes.
Challenges
Considerable design challenges are present when moving to higher voltage. These include:
- Safety – As voltage increases, more rigorous insulation and protection standards are required.
- Training – Higher voltage systems may require specialized training programs and handling equipment.
- Electromagnetic Compatibility – Higher voltage power electronics are more likely to require significant electromagnetic interference countermeasures.
- Bearing wear – With increased voltage comes greater influence from parasitic currents in isolated elements, which can lead to premature bearing failure when compared to lower voltage equivalent systems.
- Component costs – These may be higher, especially for semiconductors and connectors rated for high voltage.
- Infrastructure – The choice of battery voltage impacts the design of charging infrastructure because chargers must be compatible with the voltage requirements of the batteries they serve.
Conclusion: Why Voltage Matters
Voltage is more than just a number on a spec sheet. It is a foundational design choice that helps define the performance, efficiency, and scalability of inverter-based systems. As the demand for electrification continues to grow across mobility, energy, and industry, high-voltage inverters will be at the heart of the transition. By understanding and embracing this shift, companies and engineers alike can unlock products with superior performance, sustainability, and innovation.