Harvesters Driven by High-Voltage, Low-Power Inverters
A hybrid harvester needed an inverter for wheel motors. The original equipment manufacturer (OEM) of the hybrid harvesters and electric mowers wanted to minimize its harvester’s carbon footprint. It turned to an expert provider of power electronics to add the ideal inverter for the application
Technical Challenge
The OEM wanted to electrify multiple parts of the machine. The high voltage platform would have inverters for wheel motors. They would be used to drive the low-power wheel motors.
The Solution
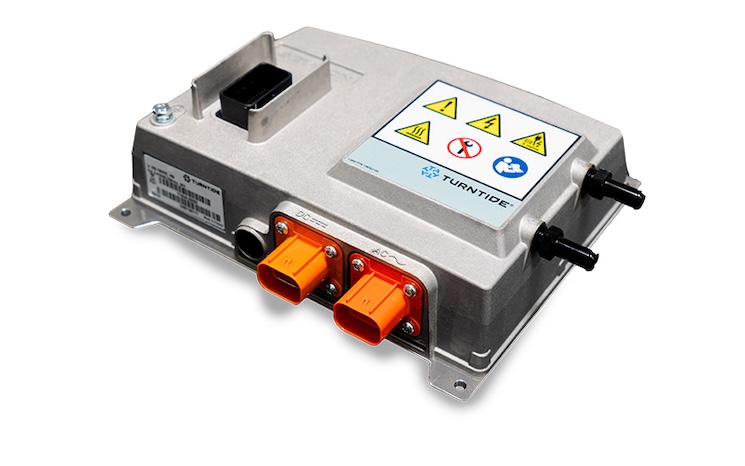
A high-voltage, low-power (HVLP) motor controller and inverter was installed to manage the wheel motors. It provided low-power delivery from a high-voltage device. It reduced the need for separate voltage conversion states.
The specifications for the HVLP inverter are:
- Nominal voltage, 700 volts direct current (VDC)
- 100% derating voltage, 800 VDC
- Minimum battery voltage, 128 volts
- Peak current at 1 minute, 53 amps root mean square (Arms)
- Continuous for 60 minutes 33 Arms
The Results & Performance of the Inverter for Wheel Motors
This HVLP motor controller for the harvester was a success. It extended the machine’s operating range. The controller also provided better efficiency and lower cost to the OEM.